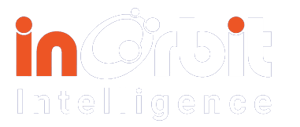
FAQ
Frequently Asked Questions
InOrbit Intelligence consulting services are designed to meet the needs of companies deploying smart robots, regardless of where they are on their journey. Here we explore answers to some of the most common questions we receive about robots and their implementation into production environments.
This page is in development and growing regularly. If you have a question about robots please let us know and we'll add it to our list.
To ensure you make the most out of your investment in robotics, you may want to consider the following key factors: Process, Disruption, Future Proofing and ROI. Let’s elaborate on those.
Firstly, thoroughly understand your processes and identify areas for improvement, particularly those involving manual labor and material transportation. Assess payloads and routes to determine your pain points which will help identify the type of hardware required for optimal performance.
Secondly, decide how much disruption you can accommodate during deployment. Evaluate whether you can afford to temporarily shut down operations or if a phased deployment while running at full capacity is necessary. This will determine the level of autonomy needed, with AGVs being less autonomous but more efficient, and AMRs offering minimal disruption but also slightly less efficiency in strictly timed operations situations.
Additionally, plan for future scalability and interoperability. Introduce an interoperability platform along with your initial fleet deployment, ensuring seamless integration as you introduce more robots and technologies into your operations. Scalable integration capabilities, especially with your Warehouse Management System (WMS), Robotic Process Automation (RPA), and IoT devices, are essential for future success.
Consider your investment objectives, whether strict ROI, initial cost optimization, scalability, or productivity gains. This will guide the choice of business models, such as Robotics-as-a-Service (RaaS), and help determine the vendors you engage with.
By addressing these factors, you can make informed decisions to maximize the benefits of your robotics investment and achieve long-term success.
The logistics and supply chain industry is witnessing a significant transformation driven by robotics and automation. Warehouse automation has been on the rise for the last 10 years, with the adoption of new technologies such as autonomous mobile robots (AMRs) and IIOT infrastructure to automate tasks like sorting, packing, and palletizing. Robotic Process Automation (RPA) is streamlining administrative tasks, while last-mile delivery robots are enhancing efficiency in the final stage of delivery. Collaborative robots (Cobots) are working alongside humans in warehouses, assisting with mundane and dull tasks. Additionally, AI is optimizing supply chain operations through data analysis, prediction of demand patterns, and route planning.
When evaluating Autonomous Mobile Robots (AMR) or Autonomous Guided Vehicles (AGV), several pivotal factors come into play. Payload, Safety, Throughput and Integration capabilities are some of the most important things to consider. Here are some questions to ask when starting to think about what AMRs are the best fit for your operation.
Payload: What kind of items are being moved?
Individual items or SKUs (Eaches) and small loads typically fit well in the <100 Kg payload category, but larger payloads and palletized goods might require different kinds of robots. In many situations, you may encounter mixed fleets with robots from different vendors taking care of varying payloads. This is when an Interoperability platform should be considered to make sure your deployment is scalable and future-proof the initial investment.
Safety: What are the safety regulations that apply to the given process?
A good place to start is the set of safety requirements for industrial mobile robots ANSI/RIA R15.08-1-2020, but there might be other regulations applying to your sector depending on your expected payloads.
Throughput: Is Speed more important than Deliverability and Completion?
Not all operations are made equal. While some may require items to arrive right on time, for example delivering parts to a manufacturing line, others may require the items to be delivered in complex environments that require the robots to improvise new paths. This key difference will help you decide if you need an AGV (likely for the first scenario) or an AMR (ideal for changing environments). Either way, integrating those robots with the rest of your industrial equipment will be crucial to the success of the operation.
Integration: multiple robot vendors? IoT devices? WMS, WCS?
Robots are almost never fully isolated. They interact with the world around them through their sensors and actuators and they need to communicate with other robots, different machines and even other layers of software to accomplish their tasks. This level of automation can only be achieved by enabling your robots to interact with all of those devices. There are many ways to achieve this goal, so properly evaluating the advantages and disadvantages of custom middleware or a scalable platform solution is critical.
When transitioning from an Autonomous Mobile Robot (AMR) pilot to a full-scale production deployment, a strategic approach is essential to ensure a seamless and successful transition. Below are key steps to guide you through the process:
Start Small and Diversify Vendors
Begin the scaling process by deploying a limited number of AMR units. This initial phase is crucial for understanding both the strengths and weaknesses of the chosen AMRs. To avoid vendor lock-in and increase flexibility in the long run, consider involving multiple vendors from the outset. Each vendor's AMRs may have unique features and capabilities that can cater to different requirements within your production environment.
Establish a Comprehensive Support Plan
Even the most advanced AMRs can experience occasional glitches or require assistance. It's imperative to have a well-defined support plan in place. This can involve either partnering with a third-party support company specializing in AMRs or thoroughly training your internal team to handle incidents promptly and effectively. The support plan should encompass troubleshooting procedures, maintenance schedules, and access to the right tools and spare parts.
Define Key Performance Indicators (KPIs) and ROI
Before expanding your AMR deployment, identify the KPIs that matter most to your operation's efficiency and success. Whether it's throughput, cycle time, accuracy, or labor savings, clearly define these metrics. Calculating the Return on Investment (ROI) for a full-scale deployment is crucial. Determine where the cost savings and operational improvements will arise, and align these benefits with your organization's goals.
Design for Throughput and Flexibility
Design the production system with both optimal throughput and adaptability in mind. AMRs can significantly enhance efficiency, but only if the production layout and processes are optimized for their integration. Plan the layout to ensure smooth navigation, efficient picking, and safe interaction between robots and human workers. Moreover, maintain a level of flexibility in the system to accommodate changing demands and scenarios. AMRs should seamlessly adjust to varying tasks and production volumes.
Gradual Expansion and Continuous Improvement
Scaling up to a full production deployment should be a gradual process. Expand the AMR fleet incrementally, allowing your team to adapt to the changes and learn from each phase. This approach minimizes disruption and enables you to make necessary adjustments based on real-world experiences. Continuously gather feedback from operators and gather data on the AMRs' performance to refine the deployment strategy over time.
Transitioning from an AMR proof of concept to a successful production deployment requires a meticulous approach. By starting small, diversifying vendors, planning for support, defining KPIs, designing for throughput and flexibility, and pursuing gradual expansion, you can ensure a smooth and efficient integration of AMRs into your production environment. At InOrbit we have the experience and tools to make you successful and maximize the benefits of AMRs into your process.
More questions and answers coming soon!
Explore InOrbit Intelligence in more detail here.